Aluminum-silicon alloys have a low melting point and good fluidty, so it is suitable for use as solder. The typical aluminum brazing alloys are 4343, 4045 (US brand) and 4004 alloy. Industrial pure aluminum, aluminum-manganese alloys and aluminum-magnesium-silicon alloys such as 6951 (US brand) alloy have good brazing properties, and they can be brazed with the above-mentioned aluminum-based solder.
6061, 6053 (US brand) and 6063 alloys in the aluminum-magnesium-silicon series also have good brazing properties, but because their starting melting temperatures are lower than those of industrial pure aluminum and aluminum-manganese alloys, the brazing temperature must be strictly controlled to prevent overburning.
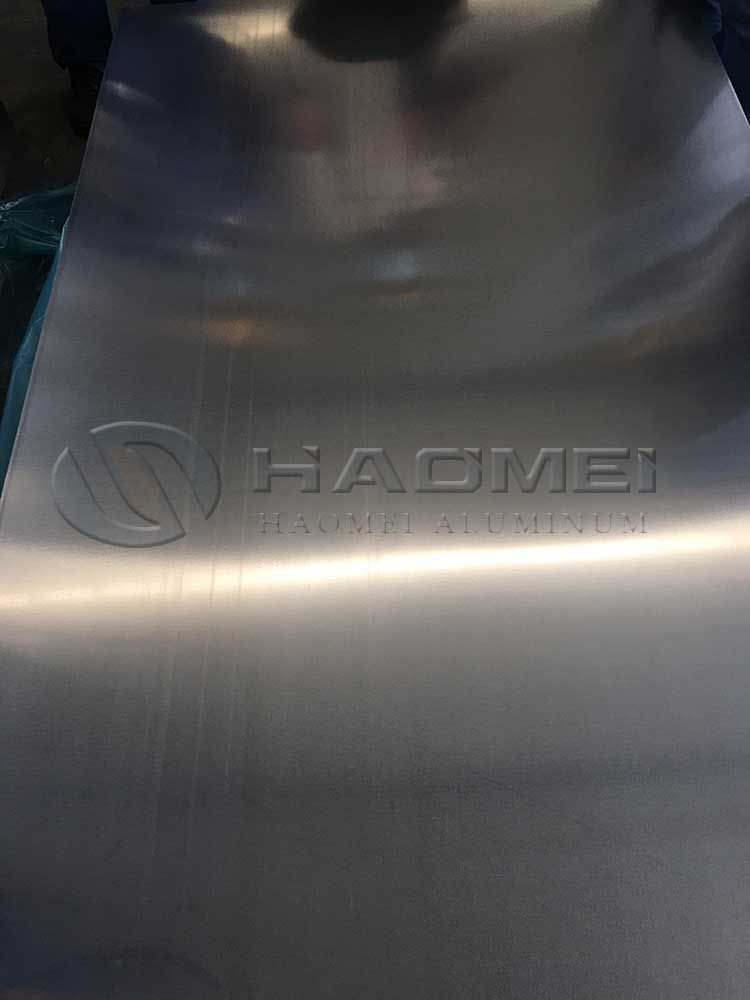
4004 brazing filler metal contains magnesium and is suitable for use in vacuum brazing. During the brazing process, the magnesium vapor reacts with the remaining oxygen and water in the furnace to purify it. The magnesium vapor also inhibits the re-oxidation of the aluminum alloy being brazed.
Aluminum alloy brazing plates are usually composite plates composed of an aluminum-manganese alloy (Chinese brand 3A21, 3003) core material and an aluminum-based solder cladding layer.
The manufacturing process is to place the aluminum-based solder plate on one or both sides of the core material ingot, preheat it to the hot rolling temperature (about 500°C), hot-roll it, and then cold-roll it into a thin plate. The cladding is completely pressed to the core material. The thickness of the cladding layer is 5% to 15% of the thickness of the core material. They are widely used in the manufacture of various heat exchangers.
Aluminum alloy brazing mainly includes the following processes:
1. Flame brazing
Flame welding is generally used in small parts, low-volume production and nail welding of aluminum combinations. Because the melting point of the solder is close to the melting point of the base metal, special care must be taken to avoid overheating the base metal.
2. Brazing in furnace
When using flux, aluminum alloys can be brazed in a furnace in an air atmosphere, but a controlled atmosphere is better. As the moisture content is eliminated during the drying process, flux-free brazing can be achieved.
3. Brazing in air furnace
Brazing furnaces used for brazing aluminum alloys have many similarities with heat treatment furnaces used for aluminum alloys. These devices are designed to operate in a temperature range below 650°C with a temperature control accuracy of ±3°C (e.g. 650°C ±3°C).
4. Inert gas brazing
Various designed furnaces can be brazed with inert gas. Before using the inert gas flushing system, water molecules must be removed from the surface of the workpiece using a combination of heating and evacuation.
5. Brazing in vacuum
Aluminum alloys can be brazed in a vacuum without flux. Furnaces with a vacuum degree of 10-6~10-5 are often used in conjunction with magnesium, which acts as a denaturant to absorb gaseous oxygen, oxide films and aluminum.
6. Brazing of dissimilar metals
Aluminum is capable of being brazed with other metals. Titanium, nickel, cobalt and beryllium can be directly brazed with aluminum; copper and brass cannot be brazed directly with aluminum and aluminum alloys and require special measures to weld.
Haomei Aluminum provides 4343, 4045, 4047, 3003 and industrial pure aluminum sheet and strip for aluminum brazing. Welcome to leave message below to inquire what you need.