In recent years, with the rapid development of the lithium battery industry, the requirements for the cruising range of automobiles have gradually expanded, and the requirements for battery energy density have also become higher and higher. For current collectors, reducing thickness and weight is one of the key research and development directions. The positive battery aluminum foil has been reduced from 15-20μm a few years ago to 8-10μm today.
The battery aluminum foils developed in the early stage are mostly aluminum-based alloys such as 1070, 1235, and 1100. If you want to increase the energy density of the battery, you need to increase its tensile strength and elongation while reducing the thickness of the aluminum foil.Therefore, the development of diversification and high strength of alloys is the main research and development direction in the future.
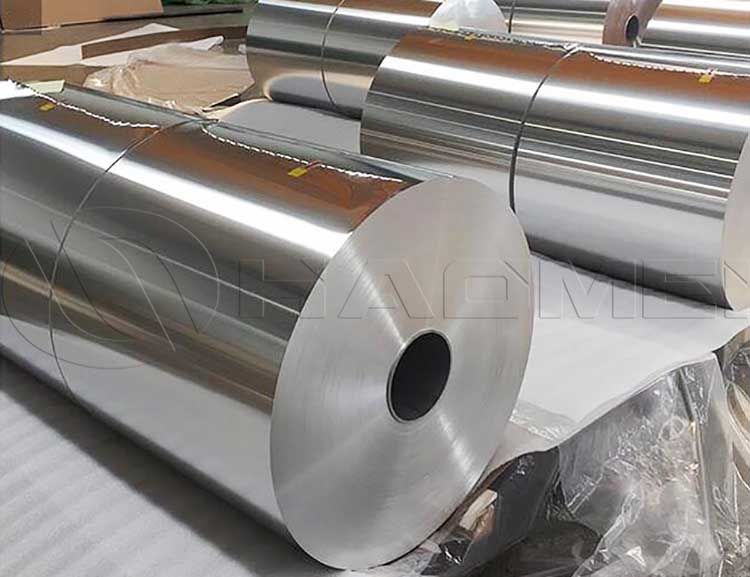
Battery aluminum foil is the basic material for battery production. In recent years, with the development of lithium-ion batteries, aluminum foil has been applied to the positive current collector of the core component of lithium batteries due to its good electrical conductivity. Lithium batteries use aluminum foil for the positive electrode and copper foil for the negative electrode, and the cost of aluminum foil accounts for 2-3% of the cost.
In sodium batteries, since sodium does not react with aluminum, aluminum foil is used for both positive and negative electrodes, and aluminum foil accounts for about 5% of the cost. Due to the lower price of aluminum, lower density and no need for charging and transportation, the use of aluminum foil can reduce cost and transportation cost.
Battery aluminum foil has more requirements than traditional aluminum foil in various aspects. First, high cleanliness. There is no debris, dust, especially iron filings. Second, high shape requirements. The uniformity of the positive electrode material coated on the surface of the aluminum foil will greatly affect the service life and battery life of the lithium-ion battery. Usually, the shape of the plate needs to be controlled below 101.
Third, high mechanical performance requirements. In the case of ensuring the purity of aluminum, it is required to have high tensile strength and high elongation, and the elongation rate is required to be greater than or equal to 3%. In fact, it is difficult to have both.
Forth, high thickness and pinhole requirements. The thickness difference requirement is less than ±3%. However, the reduction in the thickness of the aluminum foil will inevitably lead to an increase in the number of pinholes, which will increase the possibility of breaking the tape during the rolling process and seriously affect its quality.
Fifth, high surface requirements. The surface of the aluminum foil must not have various surface defects such as bright spots on the dark side, black oil lines, pitting, etc. This is directly related to the uniform coating and compaction process of the lithium-ion battery. The requirements on the cleanliness of the aluminum foil machine and the environment is very high.
Sixth, high dyne value. In order to ensure the coating quality, the dyne value on the surface of the aluminum foil should reach more than 31 dyne, and some customers even require more than 33 dyne.
Haomei Aluminum is a special battery aluminum foil supplier. We have 1060, 10740, 1235, 3003 and 1100 aluminum foil. Welcome to leave message below to inquire what you need.