Which Aluminum Alloys Are Used in Battery Manufacturing
Publish Time: 2024-02-22 Origin:https://www.hmaluminumsupply.com
The cathode current collector aluminum foil of high-end power batteries has a high technical content. The alloys of the battery aluminum foil are mainly 1060, 1070, 1100, 1235 and 3003. The mainstream thickness specification is 10-20μm, and some battery manufacturers use 8μm. The future direction is to continue to thin, and the aluminum foil thickness may even be reduced to 6μm.
AA3003 aluminum foil belongs to the aluminum-manganese alloy. Its strength is higher than that of 1xxx aluminum foil and 10% higher than 1100 and 1060 aluminum foil. 3003 electronic foil has good formability and is mainly used in deep stamping. The power battery casing made of 3003 aluminum foil is impact resistant, not easy to break and leak, and can meet the strength and rigidity requirements of the power battery casing.
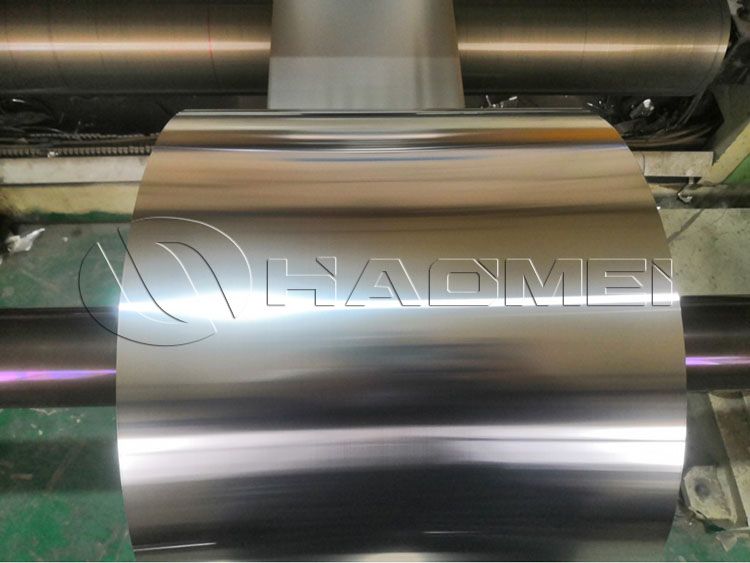
1235 aluminum foil is a commonly used aluminum foil. The aluminum content of 1235 aluminum foil is more than 99.35%. It is also a kind of pure aluminum foil and is widely used in cables, aluminum tapes and battery foil. The alloy composition of 1235 aluminum foil is different from that of 8011 aluminum foil. The difference in process lies in the different annealing temperature. The annealing temperature of 1235 aluminum foil is lower than that of 8011 aluminum foil, but the annealing time is basically the same.
Currently, aluminum foil is mainly prepared by calendering. The main product categories include packaging aluminum foil, air conditioning aluminum foil, electronic aluminum foil, battery aluminum foil, etc.
Generally speaking, the process difficulty of battery foil is reflected in thickness requirements, thickness accuracy requirements, strength, surface dyne value, etc. It requires the thinnest thickness, the highest strength, the highest dyne value, the smallest thickness difference, the optimal plate shape, the cleanest surface at the same time.
Generally, aluminum processing and billet process routes are mainly divided into two methods: hot rolling (DC) and continuous casting and rolling (CC), each with its own characteristics. Hot rolling has certain advantages in alloys with high element content and heat treatable alloys.
For general industrial light gauge aluminum foil like battery aluminum foil that belongs to the pure aluminum or general low-iron-silicon alloy, the continuous casting and rolling process shows a relatively great advantage.
Because of the particularity of aluminum foil for batteries and the extremely high requirements for product quality, higher requirements will be placed on the production process, production equipment and testing methods. We have established a professional production line for battery aluminum foil. The entire production line is dedicated to the production of battery aluminum foil, with special rolling mills, slitting machines, etc. Welcome to leave message below to inquire 1235 aluminum foil and other alloys.