The Effect of Alloy Element on Aluminum Brazing Material
Publish Time: 2021-12-28 Origin:https://www.hmaluminumsupply.com
Al-Si brazing material has good fluidity and wettability, and at the same time, the corrosion resistance and workability of the brazed joint are also good. Therefore, it has been widely used in the brazing of aluminum and its alloys; however, the melting point of this brazing filler metal is about 577 degrees Celsius.
If the Al-Si brazing filler metal is used to braze the lower melting point aluminum alloy such as 6063 aluminum alloy, its brazing temperature will be very close to its solidus temperature of 615 degrees Celsius, which the base material is prone to coarse grains and corrosion defects. Therefore, the development of a lower melting point aluminum-based solder has important practical significance.
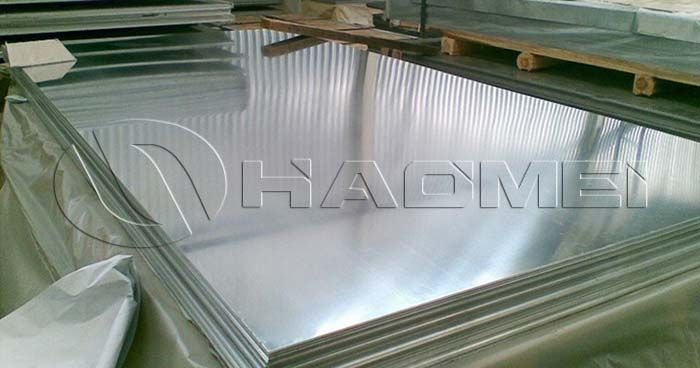
At present, mainly uses the addition of Cu to achieve the purpose of lowering the melting point. For example, the Al-Si-Cu-Ni brazing filler metal developed by Beihang University has a melting point of 535.8 degrees Celsius. At 570 degrees Celsius, it wets well with the base metal, but the solidus temperature of the solder is still relatively high.
The structure of Al-Si-Cu-Mg solder is mainly composed of a complex eutectic of matrix phase, granular phase Mg2Si, skeletal phase A12CU and Mg2Si. With the increase of Cu and Si content, the complete dendritic structure gradually disappears. When the mass fraction of Cu is 20% and the mass fraction of Si is 7.5%, the crystal grains are fine and the phases are evenly distributed.
The factors of the hardness experiment from the primary to the secondary are: Cu, Si, Mg; within the test composition range, the microhardness of the Al-Si-Cu-Mg solder increases with the increase of Cu and Si content. After the Mg content is greater than 0.8%, the hardness decreases with the increase of Mg content.
The melting point of Aluminum brazing material decreases with the increase of Cu, Si and Mg content. The results of range theory analysis show that Cu is the main factor, followed by Si, and Mg is the smallest. Al-7.5Si -20Cu -0.4Mg under the test temperature conditions, is of larger spreading area, good wetting effect with the base metal and of excellent comprehensive performance.