Electric Vehicle Heat Exchange Aluminum Sheet
Publish Time: 2025-03-07 Origin:https://www.hmaluminumsupply.com
The physical properties of aluminum provide an ideal solution for heat exchange systems: its thermal conductivity is as high as 237W/m・K, which is not as good as copper but far better than steel, and its density is only 1/3 of steel and 1/4 of copper.
By adding alloying elements such as magnesium and silicon, aluminum alloy can maintain its light weight while increasing its strength to 200-300MPa, fully meeting the structural requirements under complex working conditions. This combination of "lightweight + efficient thermal conductivity" makes aluminum alloy the preferred material for thermal management systems of new energy vehicles.
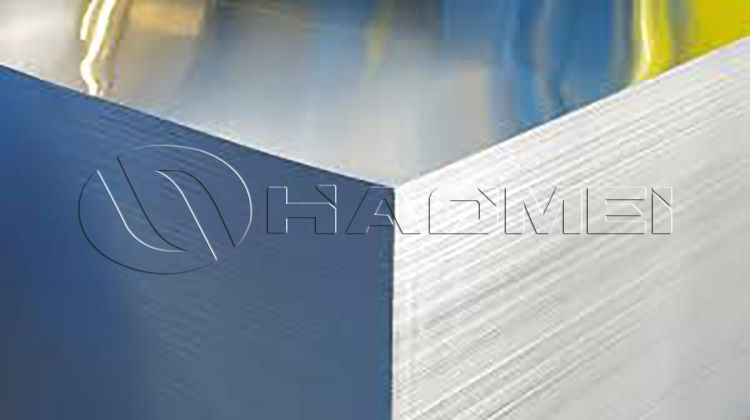
The application of automotive aluminum alloy in the field of heat exchange is developing from a single function to a diversified one. In PTC heaters, the use of aluminum plate heat exchange technology can achieve a heating efficiency of 99%.
Its glue-free bonding process not only ensures the air quality in the car, but also extends the service life to 6,000 hours. More importantly, through structural optimization, aluminum liquid cooling plates can achieve a 100% heat capture rate, significantly reducing the PUE value of data centers. This technical advantage also has broad prospects in the field of liquid cooling energy storage.
As a "veteran" material in the field of heat exchange, 3003 aluminum alloy occupies an important position with its balanced comprehensive performance. The alloy uses manganese as the main alloying element (Mn content is about 1.0-1.5%). While maintaining a high thermal conductivity of 237W/m・K, it forms a natural protective layer through the surface oxide film to resist corrosion from weakly acidic condensate. Its elongation of more than 20% allows it to be easily processed into 0.07mm ultra-thin fins, which are widely used in household air conditioners and automobile condensers.
The thermal management complexity of new energy vehicles is much higher than that of traditional models. Battery packs need to maintain stable performance in extreme environments of -30℃ to 55℃. Aluminum alloys have become ideal carriers for the integrated design of water cooling systems due to their good corrosion resistance and plasticity. For example, the use of 3003 aluminum alloy in the battery pack shell not only reduces weight by 20%, but also integrates the cooling water channel with the structural parts, increasing the thermal response speed by more than 30%.